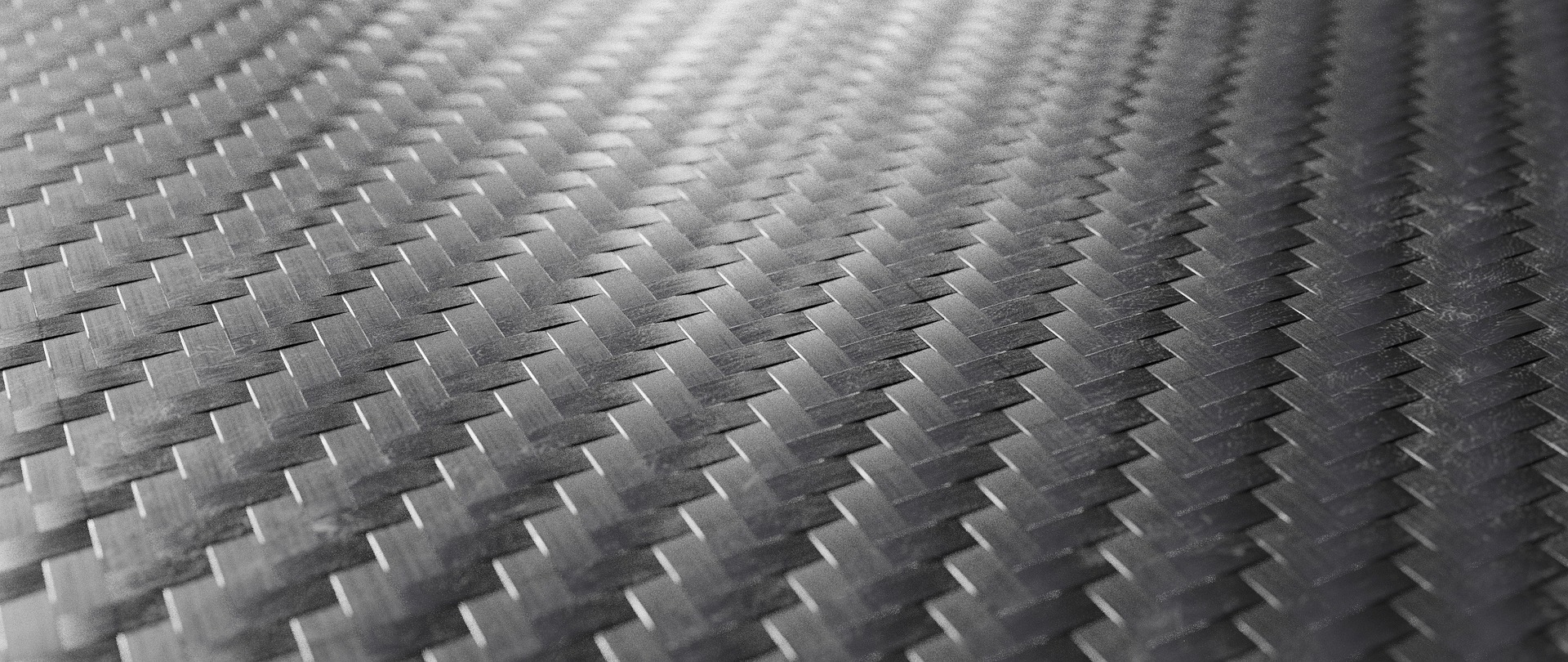
AI defect detection for carbon fiber composites
Carbon fiber is a versatile and durable material that has become increasingly popular in various industries due to its strength, light weight, and high resistance to corrosion. However, like any material, it is not immune to defects. In order to ensure the structural integrity and performance of a carbon fiber component, it is essential to regularly inspect it for defects. This process is known as carbon fiber inspection.
Carbon fiber
Carbon fiber is a type of advanced material that is made from thin fibers of carbon. These fibers are extremely strong and stiff, making carbon fiber one of the strongest and most durable materials available today.
Carbon fiber is made from a polymer called polyacrylonitrile (PAN), which is a long chain of carbon atoms with hydrogen and nitrogen atoms attached. The fibers are made by heating PAN to extremely high temperatures, which causes the carbon atoms to bond together and form a strong, crystalline structure. This process is called pyrolysis. The resulting fibers are then bundled together and held in place with a resin, which forms the carbon fiber composite material.
Carbon fiber composites are known for their high strength-to-weight ratio, which means they are extremely strong while also being relatively lightweight. This makes them ideal for use in a wide range of applications, from aerospace and automotive to sports equipment and medical devices. Carbon fiber is also resistant to corrosion, making it a good choice for use in harsh environments.
One of the most important characteristics of carbon fiber is its high stiffness. Carbon fibers are able to resist deformation under load, and therefore carbon fiber composites have a very high modulus of elasticity. This makes them ideal for use in components that need to be lightweight and stiff, such as airplane wings and racing bike frames.
Carbon fiber is also an excellent conductor of heat, which means it can be used to dissipate heat quickly, which is a crucial feature for electronic devices that generate heat. Carbon fibers has a high thermal conductivity which is four times that of aluminum.
There are two main types of carbon fiber: PAN-based carbon fiber and pitch-based carbon fiber. PAN-based carbon fiber is the most commonly used type and is made from polyacrylonitrile. Pitch-based carbon fiber is made from petroleum-based precursors and has a higher thermal stability and lower thermal expansion than PAN-based carbon fiber.
Carbon fiber is a very versatile material, its properties make it useful in a wide range of applications, including aerospace, automotive, sports equipment, and medical devices. Its light weight and high strength make it an ideal material for use in structures that need to be both strong and lightweight, such as airplane wings and racing bike frames. Its high thermal conductivity makes it useful in electronic devices that generate heat. Its resistance to corrosion makes it suitable for use in harsh environments. However, it is not a cheap material, which is one of the reasons it's not used in all applications where it would be beneficial.
Overall, carbon fiber is a high-performance material that offers a unique combination of strength, stiffness, light weight, and resistance to corrosion. Its unique properties make it an ideal choice for a wide range of applications and industries.
Different methods of carbon fiber inspection
Carbon fiber inspection is typically performed using non-destructive testing (NDT) methods, which allow the component to be inspected without damaging it. One of the most commonly used NDT methods for carbon fiber inspection is ultrasonic testing (UT). UT uses high-frequency sound waves to detect defects in the material. By sending sound waves through the material and analyzing the echoes that are returned, technicians can determine the presence and location of any defects.
Another popular NDT method for carbon fiber inspection is visual inspection. Visual inspection involves using the naked eye or a microscope to examine the surface of the material for defects. While it is not as sensitive as UT, visual inspection is quick and simple, and can detect surface-level defects such as cracks, delaminations, and voids.
Infrared thermography is a non-contact method that uses infrared cameras to detect defects by sensing the differences in temperature within a component. It is widely used in detecting the defects in composite materials including carbon fiber.
Radiography is yet another method which uses X-ray to inspect the material for defects. This method can detect internal defects such as voids or inclusions. But this method has a disadvantage of exposing the component to ionizing radiation.
Carbon fiber inspection is an important step in the maintenance and repair of carbon fiber components. By regularly inspecting the material for defects, it is possible to detect and repair problems before they cause damage or failure. This can help to ensure the safety and performance of the component, as well as extend its service life. When it comes to carbon fiber inspection, it is important to choose the right NDT method, as well as to have experienced technicians perform the inspection to ensure accurate results.
Data labeling
The annotation of image and video data is a crucial step in the development of machine learning models for computer vision tasks. However, manually annotating large datasets can be time-consuming and labor-intensive. This is where cloud-based annotation tools come in. These tools provide a web-based interface that allows users to easily label objects, regions, and attributes within image and video data. By hosting the data and the tool on a remote server, cloud-based annotation tools allow for easy collaboration and parallel annotation, which can significantly speed up the annotation process.
One of the most popular cloud-based annotation tools is CVAT (Computer Vision Annotation Tool). CVAT is an open-source tool that provides a simple, intuitive interface for annotation, making it easy for users to label objects and regions within images and videos. The tool supports annotation of rectangular and polygonal regions, as well as attributes such as object class and attributes, which can be used for training machine learning models. Additionally, CVAT provides support for multiple users and allows for annotation to be done in parallel, which can greatly speed up the annotation process.
The use of cloud-based annotation tools like CVAT can significantly improve the accuracy of machine learning models. By providing a consistent, high-quality annotation, these tools can ensure that the training data is accurate and unbiased, which leads to more accurate machine learning models. Additionally, cloud-based annotation tools are more scalable and can handle larger amounts of data, allowing for annotation of large datasets without the need for expensive hardware.
Cloud-based annotation tools also provide improved security for the data, as the data is stored on remote servers with strict access controls. This ensures that the data is protected from unauthorized access and is not subject to data breaches.
In conclusion, the use of cloud-based annotation tools like CVAT is essential for the development of accurate and reliable machine learning models for computer vision tasks. These tools provide a simple, intuitive interface for annotation and allow for easy collaboration and parallel annotation, which can significantly speed up the annotation process. Furthermore, the use of cloud-based annotation tools can improve the scalability and security of the annotation process, making them an essential tool for computer vision research and development.
Segmentation of carbon fiber defects
Convolutional neural networks (CNNs) have proven to be a powerful tool for image segmentation, particularly for segmenting defects in carbon fiber composites. CNNs are a type of deep learning algorithm that can learn to recognize patterns in images and can be trained to perform segmentation tasks.
When it comes to segmenting carbon fiber defects, CNNs can be trained to identify various types of defects such as cracks, delaminations, and voids, even if they are small or difficult to see with the naked eye. The training data for the CNNs should include images of carbon fiber samples with and without defects, as well as annotations that indicate the location of defects in the images.
Once trained, the CNN can be used to segment new images of carbon fiber samples, providing a segmentation map that indicates the location of any defects in the sample. This map can then be used to quantify the size and location of the defects, which can be useful information for determining the severity of the defects and the appropriate course of action.
One of the main advantages of using CNNs for segmenting carbon fiber defects is their ability to handle large amounts of data. CNNs can be trained on thousands of images, allowing them to learn to recognize a wide variety of defects. Additionally, CNNs can be fine-tuned for different types of defects and for different types of carbon fiber composites.
Another advantage of using CNNs is their ability to handle images with varying lighting conditions, which can be an issue when trying to segment defects in carbon fiber composites. CNNs can be trained on a diverse set of images, allowing them to recognize defects under different lighting conditions.
Model deployment
A web-based application for semantic segmentation of carbon fiber defects using deep learning can be a powerful tool for manufacturers and operators of carbon fiber composite products. This application can use state-of-the-art deep learning techniques to detect and classify defects in carbon fiber samples, making it possible to detect and repair defects early on, minimizing the risk of costly repairs or even total failure of the product.
The application would have a user-friendly interface that allows users to upload images of carbon fiber samples and view the segmentation results. The images would be analyzed using a deep learning model that has been trained for semantic segmentation of carbon fiber defects. The model would be capable of recognizing various types of defects such as cracks, delaminations, and voids, even if they are small or difficult to see with the naked eye.
The output of the model would be a segmentation map, where each pixel is assigned a class label indicating whether it is a defect or not. The map can also be color-coded to indicate the specific type of defect. The user can view the segmentation results by overlaying the segmentation map onto the original image.
The application would also have a reporting feature that generates a report indicating the location, size, and type of defects found in the image. This report can be exported in a variety of formats, such as pdf or csv, for further analysis and documentation. This information can be used to assess the severity of the defects and the appropriate course of action.
One of the main advantages of this web application is that it would provide a consistent and efficient method for detecting and classifying defects in carbon fiber samples. The deep learning model would be able to detect and classify defects with high accuracy, reducing the chance of human error. Additionally, the application would allow multiple users to access the model and use it to analyze their own images, which can greatly speed up the inspection process.
Another advantage of this web application is that it would be scalable and accessible to users regardless of their location. As the model and the application would be hosted on a remote server, users could access it from any location and the computation power could be scaled up as needed.
Conclusion
In conclusion, automated visual inspection is a powerful tool for detecting defects in carbon fiber composites. This technology utilizes advanced algorithms and machine learning techniques to analyze images of the material and detect defects with high accuracy.
One of the biggest advantages of automated visual inspection is its ability to perform inspections quickly and consistently. Unlike manual inspections, which can be time-consuming and subject to human error, automated visual inspection allows for the rapid and efficient inspection of large numbers of components. This can be especially useful for manufacturers and operators of carbon fiber composite products, as it allows them to detect defects early on, minimizing the risk of costly repairs or even total failure of the product.
Another benefit of automated visual inspection is its ability to detect a wide range of defects, from surface-level cracks and delaminations to internal voids and inclusions. This is particularly important for carbon fiber composites, as they are known to be sensitive to small defects that can significantly impact the structural integrity of the material.
Automated visual inspection can also be integrated with other NDT methods such as ultrasonic testing and infrared thermography, to obtain a comprehensive understanding of the overall condition of the material. This can help to ensure that all defects are detected and can be repaired before they cause damage or failure.
In conclusion, automated visual inspection is a powerful tool for detecting defects in carbon fiber composites. It allows for the quick and consistent inspection of large numbers of components and can detect a wide range of defects that can affect the structural integrity of the material. By integrating automated visual inspection with other NDT methods, manufacturers and operators can obtain a comprehensive understanding of the overall condition of the material, which helps to ensure that all defects are detected and repaired before they cause damage or failure.